Concrete is one of the most widely used construction materials, but when it comes to marine environments, standard concrete just won’t cut it. Marine concrete is specially designed to withstand the harsh conditions of seawater, tidal zones, and coastal structures.
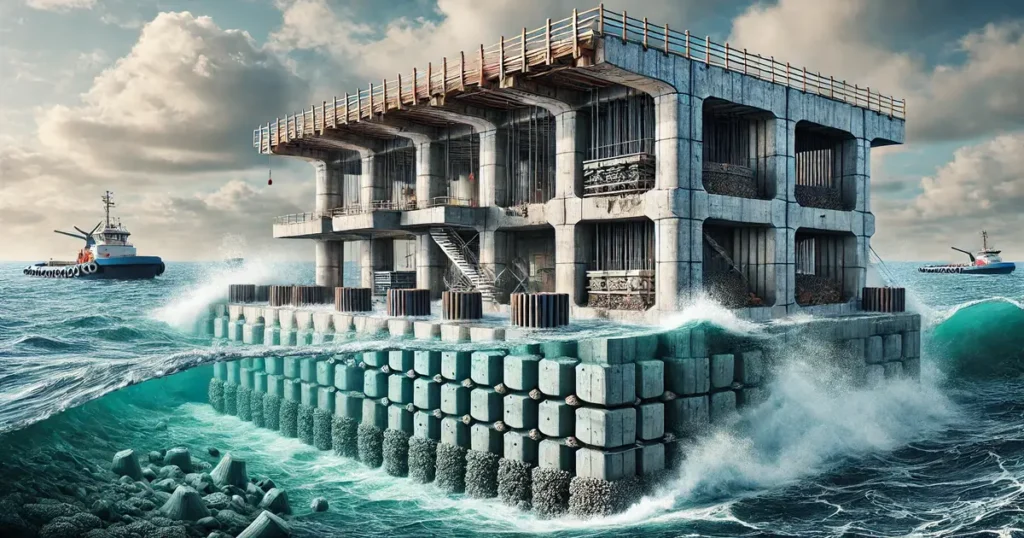
In this detailed guide, we’ll explore:
- What marine concrete
- How it differs from normal concrete
- The best cement types for marine use
- Marine concrete mix design and specifications
- Common mix ratios
- Pricing factors
What is Marine Concrete?
Marine concrete is a specialized type of concrete formulated to resist degradation caused by seawater, chlorides, sulfates, and tidal abrasion. It is commonly used in:
- Ports and harbors
- Offshore platforms
- Bridges and piers
- Coastal retaining walls
- Sewage and water treatment plants
Unlike standard concrete, marine concrete has enhanced durability due to its low permeability, high chemical resistance, and corrosion protection for reinforcement steel.
Key Challenges in Marine Environments
- Chloride Attack – Seawater contains chlorides that penetrate concrete, corroding steel reinforcement.
- Sulfate Attack – Sulfates in seawater react with cement compounds, causing expansion and cracking.
- Abrasion & Erosion – Waves, tides, and floating debris wear down concrete surfaces.
- Freeze-Thaw Cycles – In colder climates, water ingress leads to cracking due to repeated freezing and thawing.
Marine concrete is designed to combat these issues through careful material selection and mix design.
Difference Between Marine Concrete and Normal Concrete
Property | Marine Concrete | Normal Concrete |
---|---|---|
Permeability | Very low (to prevent chloride ingress) | Moderate to high |
Cement Type | Sulfate-resistant or blended cement | Ordinary Portland Cement (OPC) |
Water-Cement Ratio | 0.40 or lower | 0.45–0.60 |
Admixtures | Corrosion inhibitors, superplasticizers | Standard plasticizers (if any) |
Durability | 50+ years in seawater | 20–30 years (shorter in harsh conditions) |
Cost | 20–40% higher than standard concrete | Lower cost |
Why Normal Concrete Fails in Marine Conditions
- OPC reacts with sulfates, forming expansive compounds that crack the concrete.
- Higher permeability allows chloride penetration, leading to rebar corrosion.
- Lack of protective measures like pozzolanic additives reduces long-term durability.
Marine concrete overcomes these weaknesses through optimized mix design and material selection.
What Type of Cement is Used for Marine Concrete?
The right cement type is critical for marine durability. Common options include:
1. Sulfate-Resistant Portland Cement (SRPC)
- Contains low C3A (tricalcium aluminate) to resist sulfate attack.
- Used in high-sulfate environments (e.g., seawater with >1500 ppm sulfates).
2. Portland Pozzolana Cement (PPC)
- Contains fly ash or silica fume, reducing permeability and improving chloride resistance.
- Enhances long-term strength and durability.
3. Blended Cements (IS 456:2000 Recommendations)
- Fly Ash-Based (Class F): Reduces heat of hydration and permeability.
- GGBS (Ground Granulated Blast Furnace Slag): Improves sulfate resistance and reduces chloride diffusion
4. High-Performance Concrete (HPC) with Microsilica
- Microsilica (5–10% of cement weight) fills micro-pores, making concrete nearly impermeable.
- Used in extreme marine conditions (e.g., offshore oil rigs).
Marine Concrete Mix Design
A well-designed marine concrete mix ensures:
- Low water-cement ratio (≤0.40) – Reduces porosity.
- High cement content (400–450 kg/m³) – Enhances strength and durability.
- Pozzolanic additives (fly ash, GGBS, silica fume) – Improve chemical resistance.
- Superplasticizers – Maintain workability despite low water content.
Example Mix Design (As per IS 456:2000 for Marine Exposure)
Component | Quantity (kg/m³) |
---|---|
Cement (SRPC or PPC) | 400–450 |
Fine Aggregate (Sand) | 600–650 |
Coarse Aggregate | 1100–1200 |
Water | 160–180 (W/C = 0.40) |
Fly Ash/GGBS | 20–30% of cement |
Superplasticizer | 1–2% of cement |
Key Considerations:
- Aggregate Quality: Must be hard, non-reactive, and well-graded.
- Curing: Extended moist curing (14+ days) to prevent early-age cracking.
Marine Concrete Specifications
Marine concrete must comply with international standards such as:
- BS 6349 (Marine Structures) – Specifies durability requirements.
- ACI 318 (Marine Exposure Class) – Defines exposure conditions and material limits.
- IS 456:2000 (Indian Standard) – Recommends minimum cement content and max W/C ratio.
Critical Specifications:
- Compressive Strength: Minimum M40 (40 MPa) for severe marine exposure.
- Chloride Diffusion Coefficient: < 5 x 10⁻¹² m²/s (tested via Rapid Chloride Permeability Test).
- Cover to Reinforcement: Minimum 75 mm for submerged zones, 50 mm for splash zones.
Marine Concrete Ratio
A typical marine concrete mix ratio for M40 grade:
- Cement : Sand : Coarse Aggregate = 1 : 1.5 : 2.5
- Water-Cement Ratio = 0.40
Why this ratio works:
- High cement content ensures dense microstructure.
- Low W/C ratio minimizes capillary pores.
- Balanced aggregates provide strength and workability.
Marine Concrete Price
Marine concrete is 20–40% more expensive than standard concrete due to:
- Special cement (SRPC, PPC) costs 10–15% more than OPC.
- Pozzolanic additives (fly ash, silica fume) increase material costs.
- Quality control and testing add to project expenses.
Estimated Cost Breakdown (2024 Data)
Component | Cost (INR/m³) | Cost (USD/m³) |
---|---|---|
Standard Concrete (M30) | 5,000–6,000 | 60–72 |
Marine Concrete (M40) | 7,000–8,500 | 84–102 |
Factors Affecting Price:
- Location (coastal projects may have higher logistics costs).
- Project scale (bulk orders reduce per-unit cost).
- Admixture type (silica fume is costlier than fly ash).
Case Study: Marine Concrete in Mumbai Coastal Road Project
The Mumbai Coastal Road Project (India) uses marine-grade concrete for its 10-km sea bridge. Key takeaways:
- Cement Type: PPC with 25% fly ash.
- Mix Design: M45 grade with W/C ratio of 0.38.
- Durability Measures: Epoxy-coated rebars + 75 mm cover.
- Cost: ~INR 8,200/m³ (~$100/m³).
Results:
- Chloride penetration reduced by 60% compared to OPC concrete.
- Expected service life: 100 years with minimal maintenance.
Final Thoughts
Marine concrete is a necessity, not a luxury, for coastal and offshore structures. By using low-permeability mixes, sulfate-resistant cement, and pozzolanic additives, engineers can ensure long-term durability against seawater damage.
While it costs more upfront, the extended lifespan and reduced maintenance make marine concrete a cost-effective choice for harsh environments.